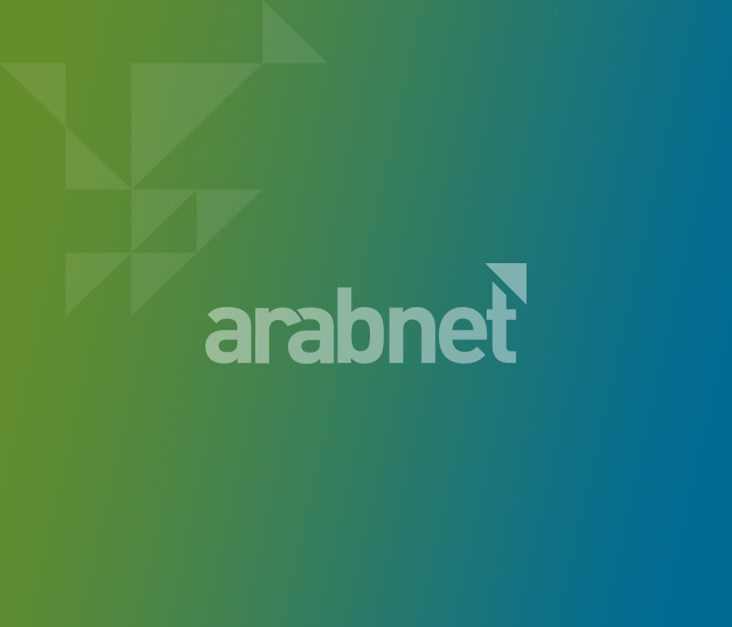
Have you ever walked through a museum, already irritated because you were dragged there against your will, and thought “this would be so much cooler if the artist had done this one thing differently”? People at the Metropolitan Museum of Art wish you would, so they hosted a 3D Hackathon where the public was invited to come in, scan works of arts, and make all the alterations they want. How? With 3D printing, a rapidly advancing, new class of cost-cutting manufacturing methods that make it possible to bring ideas previously restricted to the realm of imagination into reality.
The concept behind 3D printing is fairly simple: make things automatically with computers (especially computer aided drafting, or CAD). Traditionally, this was achieved by processes where material is removed from a solid, or pouring liquid material into molds where they then solidify. 3D printing instead is additive; objects are built piece by piece, minimizing waste and allowing for complexity impossible with other techniques. As Fab@home, a domestic-use 3D printing project, implores its users, “join us and make Anything.”
Well, if constructing any object you want out of goo sounds a bit scifi-ish, it's probably because it is. Printing is limited not only by which materials can be used, but also by the virtual blueprints used by the machines. The sky is not yet the limit, but all of a sudden everything from sculpture to manufacturing to construction has straddled the traditional boundaries between professional and personal, customized and mass-produced.
The technology is hardly new, dating back to the 1980s when it was used for quickly producing models and prototypes. Recently, though, printing techniques have advanced enough to move 3D printing from production aids to production lines. Some of these methods include selective laser sintering, which uses lasers to solidify precise locations in a liquid material that can later be drained, and fused polymer deposition, which melts solid materials using high heats before ejecting them in specific shapes, where they quickly re-solidify.
One of the game-changing benefits of such technology is how effectively it can be used on such a small scale. Before, every time a manufacturer wanted to make a product, he had to invest in an entire unique production line for it. Because that is costly, only very necessary or general products were cost effective.
3D printing, on the other hand, requires very little specialization in its production line, meaning one initial investment could produce countless custom products using different computer designs. This has made the playing field distinctly digital; instead of patented technologies, companies are starting to worry about intellectual property rights, and the limits to exchanging new products don't rely on cargo hull size, but rather on internet bandwidth.
High customization and little need for large and expensive industry also mean that manufacturing in places with poor infrastructure like the oil-less Middle East may be able to jump to the head of the pack. Brains, access to a computer, and a few thousand dollars are the most important requirements to becoming a manufacture with 3D printers, and a hundred-year head-start isn't necessary to get any of those things. In fact, 3D construction may make early industrialization even less necessary as it threatens to do away with the traditional limitations of building.
Of all the possible impacts of such a revolution, the most stunning may be its effect on small businesses and artists. The technology is cheap enough today that production of custom-made things can come directly from the retailer; customers can upload a design to a website and receive the finished product days later (google it). The upshot is that the advanced technology involved may become someone of a black box – it has become so complicated that if your company's printer somehow fails, your best hope is that it happens during business hours.
There are a lot of challenges that lie beneath the surface of the heady ambitions of 3D printers, including complicated computer designs and mixing materials. The digital nature of the technology, however, means that individual consumers can still benefit while the kinks are being worked out. Fab@home's community allows users to exchange designs for use at home, so at least if you can't figure out CAD software or the properties of production materials, someone on a Wiki is out there waiting to give you some answers.
Latest Business
Intelligence Report
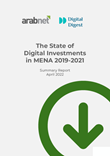